입상활성탄의 화학적 재생시 플라즈마 수중방전이 미치는 영향
Effect of Underwater Plasma Discharge on the Chemical Regeneration of Spent Granular Activated Carbon
Article information
Abstract
본 연구는 화학적 재생과 수중 플라즈마를 결합한 화학적 방법으로 폐활성탄 재생특성을 비교하여 활성탄의 화학적 재생시 플라즈마 수중방전이 미치는 영향을 조사하였다. 화학적 재생법으로는 신탄의 요오드 흡착력 대비 최대 69%까지 회복할 수 있었다. 화학적 재생에 수중 플라즈마(600 W)를 결합한 경우 화학약품만으로 재생한 경우에 비해 흡착력이 7~24% 높게 나타났다. NaOH 20%, 에탄올 50% 조건에서 수중 플라즈마(600 W)를 방사하며 48시간 반응시킨 경우 요오드 흡착력 회복률 89%를 나타내어 재생활성탄 품질기준 1등급(90% 이상)에 가까운 재생효율을 확인하였다. 흡착이 잘되는 소수성 유기물의 경우 신탄과 폐탄의 제거능이 큰 차이를 나타내지 않았으나, 소수성이 약한 유기물은 재생탄의 흡착력이 신탄에 비해 낮게 나타났다.
Trans Abstract
This study investigated the effect of underwater plasma discharge on the chemical regeneration of spent granular activated carbon (GAC). The maximum recovery rate for iodine number was 69% with chemical regeneration of the spent GAC. Chemical regeneration along with underwater plasma discharge (600 W) could achieve 7-24% higher iodine numbers comparing with the chemical alone regeneration. We could achieve 89% of iodine number recovery upon adding NaOH 20% and ethanol 50%, with discharging plasma. Adsorption of hydrophobic organic materials by both virgin and regenerated GACs exhibited similar removal rates whereas hydrophilic materials were not readily removed by the regenerated GAC.
1. 서 론
국민의 삶의 질 향상으로 먹는 물의 수질 향상에 대한 욕구는 갈수록 높아지고 있으며, 수돗물 수질이 안전하게 관리 및 공급되고 있음에도 수돗물 직접 음용을 꺼려하고 있다. 2013년 수돗물 만족도 조사결과에 의하면 수돗물을 그대로 마시지 않는 비율이 88.3%나 되었고, 수돗물을 식수로 마시지 않는 주요 원인 중 하나가 이물질 및 냄새(24%) 때문인 것으로 조사되었다. 2017년 조사결과에 의하면 냄새와 이물질 때문에 수돗물을 마시지 않는다고 답한 비율이 18.5%로 다소 감소하였으나 여전히 수돗물을 직접 마시기에는 부정적 인식이 있는 것으로 조사되었다[1].
수돗물에서 발생하는 냄새물질은 주로 미생물의 신진대사과정에서 발생되는 것으로 알려져 있으며, 그간 알려져 있는 주요 냄새물질은 흙냄새를 유발하는 Geosmin (trans-1, 10-dimethyl-trans-9-decalol)과 곰팡이 냄새를 유발하는 2-MIB (2-methylisoborneol) 등이다. 이 물질들은 응집․침전․여과공정을 이용한 표준정수공정에서 제거가 잘 되지 않으나, 입상활성탄(Granular Activated Carbon, GAC) 공정을 포함한 고도정수로 효율적인 제거가 가능하다[2~4].
활성탄에 의한 오염물질의 흡착 및 제거 기술은 효과와 적용 타당성이 입증되어 활용도가 증가하고 있으나, 운전시간이 경과함에 따라 충전된 활성탄의 세공표면 및 내부에 흡착 제거된 오염물질이 지속적으로 축적되면서 흡착대(Adsorption Zone)가 흡착지의 아래쪽으로 이동하고 흡착지 유출수의 오염 물질 농도가 점차 증가하게 된다. 이처럼 처리 목표물질 제거율이 현저히 저하되는 파과가 일어나게 되므로 입상활성탄의 흡착제거 능력 회복을 위한 재생과정은 활성탄 공정의 경제적 운영을 위해 필수적이고, 공정 설계 및 운영시 유지관리측면에서 활성탄 재생비용을 고려해야 한다[5,6].
활성탄 재생법은 크게 열 재생법과 화학적 재생법으로 구분된다. 열 재생법은 고온(900~1000℃) 가스에 의해 가열되어 가는 과정에서 수증기 증류, 탈리 혹은 열분해 후 탈리, 탄화와 같은 공정으로 흡착된 유기물을 제거하는 재생방법이며, 화학적 재생법은 저온(80~100℃)에서 화학약품을 포함한 재생용액으로 활성탄에 흡착된 물질을 분리하여 재생하는 방법이다[7]. 열 재생법은 온도 조절 및 활성화 공정이 정밀하고 연속운전에 적합하며 재생시간이 짧다. 또한 재생 중 활성탄에 2차 오염 우려가 적으며 국·내외 많은 시설에서 검증 되었다. 그러나 현장에 재생시설을 설치할 경우 유지 관리비가 화학적 재생법에 비해 높으며, 위탁 재생을 할 경우 신활성탄 가격의 70% 가량이 소요되어 비경제적이다. 또한 대기오염 물질이 배출되어 민원이 발생할 가능성이 있다[8~10]. 화학적 재생법은 재생시설이 간단하여 초기 투자비용이 적으며 운전이 간편하다는 장점이 있다. 또한 재생시 활성탄 표면 손실이 거의 없으며, 재생용량의 제한이 없다. 그리고 특별한 배가스 처리 설비가 필요 없으며, 열 재생 비용 대비 30% 정도로 경제성이 용이하다. 하지만 재생용액에 많은 비용이 소모되며 폐액처리과정이 필요하고 열 재생법 대비 긴 재생시간이 소요된다[11~14].
활성탄 재생에는 일반적으로 열 재생법이 사용되고 있으나 대기오염 및 고가의 유지비용 등의 문제가 있어 화학적 재생법에 대한 연구 및 기술개발이 진행되어 왔다. 앞서 기술한 바와 같은 화학적 재생의 단점을 극복하기 위하여 화학적 재생에 초음파, 나노촉매, 자외선 조사, 마이크로웨이브, 플라즈마를 접목하는 등 재생효율을 높일 수 있는 여러 가지 방법이 연구되어 왔다[15~19]. 이러한 다양한 방법 중 플라즈마를 결합하여 재생하는 방법은 흡착된 오염물질의 제거효율이 탁월하다는 장점이 있으나 아직까지는 연구가 부족한 실정이다.
플라즈마 방전에도 여러 방법이 있으나 화학적 재생법과 접목하기 위해서는 수중방전 플라즈마가 용이하며, 방전시 발생되는 OH라디칼과 오존을 통하여 긴 재생시간과 재생용액 감소효과를 기대할 수 있을 것이다. 수중 플라즈마는 플라즈마 전극을 수중에 위치시키고 저온에서 수중 방전을 통하여 방전열 등에 의해 물이 기화되어 생성되거나 혹은 외부로부터 주입된 미세 기포에 방전현상을 일으켜 라디칼, 즉 수산기(-OH)와 활성산소(O-, O2, O3) 및 과산화수소(H2O2) 등을 발생하는 원리이다[20,21]. 이렇게 생성된 라디칼들이 오염물질을 산화시키고, 더불어 물에 함유된 세균 및 바이러스를 살균하는 등 수질오염 정화에 폭넓게 이용될 수 있다[20,21].
본 연구는 입상활성탄의 재생을 위해 화학적 방법에 수중 플라즈마를 결합하여 기존 방법보다 재생효율을 증가시키기 위한 목적으로 기존 화학적 방법과 수중 플라즈마의 단독 또는 병합 처리시 활성탄의 재생특성을 비교하였다.
2. 연구방법
2.1. 활성탄 시료
활성탄 재생 실험을 위한 폐탄과 특성 비교를 위한 신탄은 국내 A정수장에서 사용하는 파쇄형 석탄계 입상활성탄을 사용하였다. 폐활성탄은 해당 정수장의 활성탄공정에서 약 5년 정도 사용된 것이다. 신탄은 BET (Brunauer Emmett Teller) 1165 m2/g, 요오드 흡착력 954 mg/g로 측정 되었으며, 폐활성탄은 BET 356 m2/g, 요오드 흡착력 302 mg/g, 경도(신탄 대비) 82.4%로 측정 되었다. 환경부 수처리제 기준으로 입상활성탄 품질규격은 성상(흑색 알맹이), pH 4~11, 체잔류물 95% 이상, 건조감량 5% 이하, 염화물 0.5% 이하, 비소 2 ppm 이하, 납 10 ppm 이하, 카드뮴 1 ppm 이하, 아연 50 ppm 이하, 페놀가 25 이하, ABS가 50 이하, 메틸렌 블루탈색력 150 mL/g 이상, 요오드흡착력 950 mg/g 이상 등 총 14개 항목으로 규정되어 있다[22].
2.2. 활성탄 재생실험
활성탄 재생을 위한 실험장치는 반응기와 수중방전용 플라즈마로 구성되었다. 반응기(1.5 L)에는 활성탄과 재생용액의 교반을 원활하기 위해 교반기를 설치하였고 온도를 유지하기 위한 장치로 구성하였다. 플라즈마 방전장치는 전원공급장치와 3개의 전극으로 구성되어 플라즈마 방출시 OH 라디칼 발생량을 늘릴 수 있었다. 전원공급장치는 2100 V, 출력채널 1개, 출력전압 3개로 구성되어 있고, 발열문제 해소를 위하여 냉각팬을 추가로 장착하였다. 전극의 재질은 철, 구리, 텅스텐으로 교환이 가능하다.
화학적 재생실험은 폐활성탄 10 g을 반응기에 투입 후 재생용액(NaOH 4~20%, 에탄올(C2H5OH) 10~50%)과 증류수를 1 L로 맞추고 실험조건에 따라 재생시간을 변경하며 수행하였다. 플라즈마를 활용한 재생실험은 폐활성탄 10 g을 반응기에 투입 후 증류수로 1 L까지 채운 후 실험조건에 따라 전력세기(200~600 W)와 재생시간(6~48 h)을 변경하며 실험하였다. 수중 플라즈마를 결합한 화학적 재생실험은 플라즈마를 적용한 것 외에는 화학적 재생법과 동일한 방법으로 실험하였다. 산으로 전처리 후 수중 플라즈마를 결합한 화학적 재생실험의 경우 폐활성탄을 HCl (1%)로 1시간 반응시킨 후 앞의 화학적 재생법과 동일하게 수행하였다. 각 실험에서 재생된 활성탄 시료는 세척하고 105℃에서 1시간 건조한 뒤 데시케이터에서 방냉하여 비표면적 특성을 분석하였다.
2.3. 분석 방법
폐활성탄의 재생효율 평가는 환경부 재생 활성탄 품질 평가항목 중 가장 많이 사용되는 요오드 흡착력을 중심으로 하였으며, BET, 경도 등을 추가로 분석하였다. 요오드 흡착력은 ‘수처리제의 기준과 규격 및 표시기준’에 따라 측정하였다[23]. 요오드 흡착력은 진탕배양기(ThermoStable IS-10, Daihan, Korea), 원심분리기(L530, Cence, China)를 사용하였다. 시료 0.5 g을 0.1 N 요오드 용액 50 mL를 넣고 15분간 진탕 한 후 2,000 rpm에서 5분간 원심분리 하였다. 상층액 10 mL를 비이커에 넣고, 0.1 N 티오황산나트륨용액으로 적정하여 갈색이 담황색으로 변하면 전분용액 3~4방울을 넣어 생긴 청색이 없어질 때까지 계속 적정한 후 소비된 0.1 N 티오황산나트륨용액의 적정량으로부터 요오드 흡착력을 분석하였다.
BET는 ASAP-2010 (Micrometrics, USA) 기기(dynamic flow 방법)를 이용하여 측정하였다. 105℃에서 충분히 건조한 시료 0.1 g을 시료관에 넣고 전처리 포트에 장착한 후 온도를 300℃로 유지시키면서 8~12시간 동안 50 ㎛Hg 이하의 압력에서 배기하여 세공 내 미량의 수분 및 공기를 제거하였다. 완전히 배기된 시료의 정확한 무게를 측정하고 분석포트로 옮겨 액체질소온도(77 K)에서 상대압력을 변화시켰을 때 세공분포를 조사하였다. 상대압력 0.2 이하에서 8 지점을 선택하여 BET식에 의한 비표면적을 측정하였다.
활성탄의 경도(hardness)는 규격접시(KS D 5201), 체진탕기(ORTO ALRESA, OASS203)를 사용하여 측정하였다. 지름 12.7 mm 및 지름 9.5 mm인 강구 각 15개를 체진탕기에 부착하여 30분 동안 진탕한 뒤 강구를 제외한 시료를 전부 넣어 체진탕기에 부착하고 3분 동안 진탕한 후 체 위에 남은 시료의 무게를 구하여 원래 시료 무게의 비로부터 경도를 구하였다[24]. 활성탄의 표면은 SEM (scanning electron microscope) 분석기(JSM-6500F, JEOL, Japan)로 촬영하였다.
신탄과 재생탄의 유기물 흡착능을 비교․평가하기 위하여 구미지역 지표수를 원수로 사용하였다. 유기물 성상은 fluorescence spectrophotometer (RF-5301, Shimadzu, Japan)를 이용하여 측정하고 fluorescence excitation-emission matrix (FEEM)로 평가하였다. Fluorescence spectra는 scan 분석을 통해 수집하며, excitation 파장은 220~400 nm (5 nm 간격), emission 파장은 250~600 nm (1 nm 간격)로 설정하였다. 광원은 Xenon lamp를 이용하였고, excitation-emission slit width는 10 nm로 설정하였다[25].
3. 결과 및 고찰
3.1. 화학적 재생
화학적 재생실험은 NaOH와 에탄올의 함량을 증가시키며 반응시간에 따른 요오드 흡착력을 분석하며 수행하였다(Fig. 1). 재생 활성탄 품질평가는 요오드 흡착력, 수율(%), 신탄대비 처리목표물질 제거 회복률로 하며, 항목별로 신탄대비 90% 이상의 회복률을 보이면 1등급, 80% 이상은 2등급, 70% 이상 3등급으로 평가된다[22]. 본 연구에서는 그 중 가장 대표적인 요오드 흡착력을 통하여 우선적으로 재생효율을 평가하였으며, 추가적으로 BET를 분석하여 재생효율평가의 객관성을 높였다.
Fig. 1에 나타나듯이 화학적 재생시 화학약품(NaOH, 에탄올)의 함양이 증가할수록, 그리고 재생반응시간이 증가할수록 요오드 흡착력은 증가하였다. 다만, 재생반응시간에 따른 요오드 흡착력 증가는 24시간 이후 큰 차이를 나타내지 않았다. 본 실험의 결과로 볼 때 화학적 재생시 반응시간은 24-30시간 정도가 적합하다고 판단된다. NaOH 20%와 에탄올 50%로 24시간 재생한 후 요오드 흡착력은 613 mg/g으로 증가하였고 48시간 재생한 후에는 655 mg/g으로 증가하여 폐탄에 비하여 높은 흡착력을 보였다. 그러나 본 실험조건에서 재생률(신탄의 요오드 흡착력 954 mg/g 대비)이 최대 69%로 재생활성탄 품질 3등급인 70% 이상이 되지 않아 화학적 재생만으로는 활성탄 재생이 부족한 것으로 판단된다.
3.2. 수중 플라즈마를 결합한 화학적 재생
수중 플라즈마를 결합한 화학적 재생실험은 총 세 가지 조건으로 실험하였다: (1) 수중 플라즈마만으로 재생, (2) 수중 플라즈마를 결합한 이화학적 재생, (3) 폐활성탄을 산(1% HCl)으로 전처리 후 수중 플라즈마를 결합한 화학적 재생.
첫 번째 조건인 수중 플라즈마만으로 폐탄을 재생한 것은 수중 플라즈마의 활성탄 재생 가능성을 평가하기 위해서이다. 플라즈마로만 재생한 경우 전력세기를 증가시킬수록, 그리고 반응시간이 길수록 재생된 폐탄의 요오드 흡착력이 증가하였다(Fig. 2). 전력세기 200, 400, 600 W로 48시간 재생한 경우 폐탄의 요오드 흡착력은 각각 410, 514, 584 mg/g으로 증가하였다. 플라즈마에 의해 발생된 라디칼, 즉 수산기(-OH)와 활성산소(O-, O2, O3), 과산화수소(H2O2) 등이 활성탄에 부착된 오염물질을 산화시켜 요오드 흡착력을 회복시킨 것으로 판단된다[20,21].
Fig. 2에 나타나듯이 200 W를 적용한 경우는 시간에 따른 요오드 흡착력 증가는 크지 않았고, 400 W와 600 W 조건에서는 반응시간에 따라 요오드 흡착력이 증가하다가 36시간 이후에는 반응시간 증가의 영향이 크지 않았다. 폐탄과 비교하여 수중 플라즈마 방전 후 요오드 흡착력이 증가하였으나 본 실험의 조건에서는 최대재생률(신탄의 요오드 흡착력 954 mg/g 대비)이 61%로 재생 활성탄 평가기준 3등급에도 미치지 못하였다. 따라서 수중 플라즈마 방전만으로는 활성탄 재생이 비효율적임을 알 수 있다.
다음으로 수중 플라즈마를 결합한 화학적 재생실험으로 화학약품과 수중 플라즈마로 발생되는 라디칼을 활용하여 활성탄 표면에 흡착된 오염물질의 제거를 평가하였다. 전력세기 600 W로 플라즈마를 방전시키고 화학적 재생을 수행한 경우 화학약품의 함양을 증가시킬수록, 그리고 재생반응시간이 증가할수록 요오드 흡착력은 증가하였다. 수중 플라즈마를 결합한 화학적 재생시 요오드 흡착력의 증가는 화학약품만으로 재생한 경우와 유사한 증가 경향을 나타냈으나, 회복률 수치는 화학적 재생에 수중 플라즈마를 결합한 경우가 화학약품만으로 재생한 경우에 비해 7~24% 높게 나타났다(Fig. 3). 약품주입량 NaOH 20%, 에탄올 50% 조건에서 48시간 반응시킨 경우 요오드 흡착률이 803 mg/g로 최대회복률을 나타내어 신탄의 요오드 흡착력 954 mg/g 대비 84%의 회복률을 나타내었다. 화학약품의 사용량을 줄이고 반응시간을 줄이는 것이 중요하므로 재생활성탄 품질기준 2등급 수준을 달성할 수 있는 지점을 확인한 결과 NaOH 12%, 에탄올 30%를 주입하고 36시간을 반응한 경우 요오드 흡착력 760 mg/g으로 80%를 달성할 수 있었다.
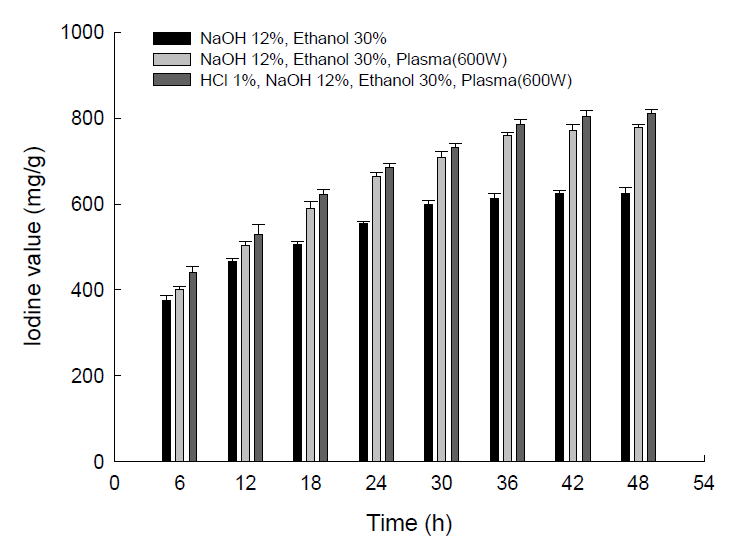
Comparison of iodine values after regeneration by chemicals (NaOH, Ethanol), chemicals (NaOH, Ethanol) with plasma discharge, and acid (HCl) pretreatment plus chemicals (NaOH, Ethanol) with plasma discharge.
세 번째, 폐활성탄을 산(1% HCl)으로 전처리 후 수중 플라즈마(600 W)를 결합한 화학적 재생을 통해 활성탄 요오드 흡착력을 평가하였다. 앞의 실험과 마찬가지로 화학약품의 함양을 증가시킬수록, 그리고 재생반응시간이 증가할수록 요오드 흡착력은 증가하였고, 회복률 수치는 수중 플라즈마와 NaOH/에탄올을 결합한 재생법에 비해 3~9% 높게 나타나 큰 차이는 없었다(Fig. 3). 약품주입량 NaOH 20%, 에탄올 50% 조건에서 48시간 반응시킨 경우 요오드 흡착률이 849 mg/g로 최대회복률을 나타내어 신탄의 요오드 흡착력 954 mg/g 대비 89%의 회복률을 나타내어 1등급(90% 이상)에 가까운 재생효율을 확인하였다.
플라즈마(600 W)와 화학적 재생(NaOH 12%, 에탄올 30%), 그리고 플라즈마를 결합한 화학적 재생(600 W, NaOH 12%, 에탄올 30%)에 의해 재생(반응시간 48 h)된 활성탄의 요오드 흡착력과 BET를 측정하여 신탄 및 폐탄의 수치와 비교하였다(Fig. 4). 요오드 흡착력과 BET는 유사한 경향을 나타냈으며, 전체적으로 BET (m2/g)가 요오드 흡착력(mg/g)에 비해 절대치 기준 50-200 가량 높은 수치를 나타내어 다른 연구와 비슷한 경향을 나타냈다[27]. 폐탄의 요오드 흡착력은 302 mg/g, BET는 356 m2/g이었고, 플라즈마를 결합한 화학적 방법으로 재생된 활성탄의 요오드 흡착력과 BET는 각각 778 mg/g, 919 m2/g이었다.

Comparison of iodine number and BET of spent, regenerated and virgin GACs (plasma 600 W; chemicals NaOH 12% and Ethanol 30%; regeneration duration = 48 h).
재생용량 증가가 수중 플라즈마를 결합한 화학적 재생에 미치는 영향을 파악하기 위해 폐탄 주입량을 증가하며 10 g과 같은 조건(NaOH 12%, Ethanol 30%, Plasma 600 W)에서 재생실험을 하였다. 10 g의 폐탄으로 실험한 경우 48 시간 반응시 요오드 흡착력이 778 mg/g이었고, 20 g의 폐탄으로 실험한 경우는 48시간 반응 후 요오드 흡착력이 775 mg/g로 비슷한 결과를 나타냈다. 폐탄 30 g을 주입한 경우 요오드 흡착력은 741 mg/g로 약 5% 가량 감소한 재생효율을 보였고, 폐탄 40 g을 주입한 경우 요오드 흡착력은 695 mg/g로 10% 이상의 감소를 보였다. 본 재생조건 하에서는 1 L 반응기 기준으로 30 g 이상의 폐탄을 재생하면 재생효율의 감소가 발생할 수 있는 것을 확인했다.
3.3. 활성탄 특성 변화
폐탄의 재생 정도를 전자현미경(SEM)으로 1000배 확대하여 촬영하여 관찰한 결과 재생 전 활성탄(폐탄)보다 화학적 재생을 한 활성탄이, 화학적 재생만 한 경우보다는 플라즈마를 결합한 화학적 재생의 활성탄이 세공이 많아지고 커졌으며, 활성탄 표면에 부착된 오염물량 또한 현저하게 줄어든 것을 확인할 수 있었다(Fig. 5). 표면 형상만으로 활성탄의 재생률을 평가할 수는 없으나 참고자료로는 활용가능하다.
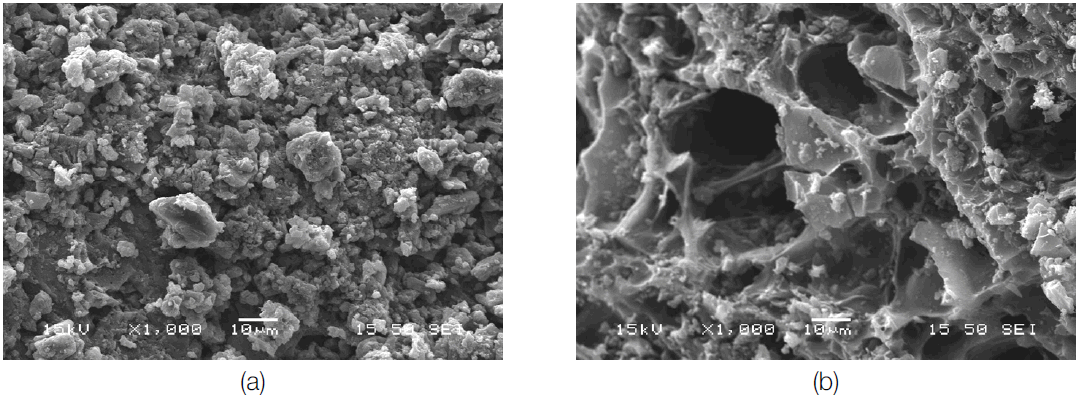
SEM images of (a) spent GAC and (b) regenerated GAC by chemicals with plasma discharge (x1000 magnification).
재생을 통해 활성탄 표면 및 세공에 부착된 오염물질이 떨어지고 흡착력이 높아지더라도 활성탄의 경도가 약해지면 흡착공정에 사용할 수 없다. 따라서 재생방법 별로 활성탄 재생 후 활성탄의 경도를 분석하였다. 신탄의 경도를 100%로 기준할 경우 폐탄의 경도는 82.4%이었고, 수중 플라즈마 재생탄(600 W)은 78.8%, 화학적 재생탄(NaOH 12%, 에탄올 30%)은 76.8%, 수중 플라즈마(600 W)와 화학적 방법(NaOH 12%, 에탄올 30%)을 결합한 재생탄은 75.5%를 나타내어 재생과정을 통해 활성탄의 경도가 어느 정도는 약해지는 것을 확인할 수 있었다. 이는 재생효율이 높을수록 활성탄에 가해지는 손실 정도가 높아져 경도가 떨어지는 것으로 판단된다[7~9].
재생탄의 유기물 제거능을 평가하기 위하여 구미지역 지표수를 취하여 흡착실험을 수행하였다. 신탄과 재생탄을 12 g/L 농도로 300분간 흡착반응시킨 후 소수성 유기물(UVA at 254 nm)의 농도감소를 측정한 결과, 신탄은 49.8%가 제거되었고 재생탄도 47.3%의 제거율을 보였다. 일반적으로 소수성 유기물(UVA at 254 nm)은 흡착에 의해 제거가 용이하다[28]. 흡착이 잘되는 소수성 유기물의 경우 신탄과 폐탄의 제거능에서 큰 차이를 나타내지 않았다.
유기물 성상에 따른 흡착특성을 보다 상세히 파악하기 위하여 FEEM을 분석하였다. 지표수의 유기물 성상에 대한 FEEM 분석에서는 주로 5가지의 fluorescence peak가 관측된다[26,29]. 신탄과 재생탄의 유기물 흡착능을 비교했을 때 fulvic acid-like (λex 237~260 nm/λem 400~500 nm)와 humic acid-like (λex 300~370 nm/λem 400~500 nm) 영역에서는 비슷한 제거율을 나타내었다(Fig. 6). 또한 tyrosine과 같은 aromatic protein 영역(λex 225~237nm/λem 309~321 nm, λex 225~237 nm/λem 340~381 nm)의 유기물도 신탄과 재생탄에서 비슷하게 흡착/제거되었다. fulvic acid-like, humic acidlike, aromatic protein 영역의 유기물은 소수성이 상대적으로 높아 흡착에 의해 제거가 용이하다. 그러나 soluble microbial byproduct-like 영역(λex 275 nm/λem 340 nm)의 유기물들은 신탄으로 잘 흡착․제거된 반면, 재생탄은 제거율이 낮았다. 신탄의 경우 이 영역의 fluorescence peak 최대값이 173으로 나온 반면, 재생탄은 최대값 301로 상대적으로 높게 나타나 soluble microbial byproduct-like 유기물에 대한 재생탄의 흡착력이 떨어짐을 알 수 있다. 이 영역의 유기물은 주로 아미노산과 탄수화물로 구성되어 있어 흡착력이 떨어진다[26,29].
4. 결 론
본 연구에서는 화학적 방법 단독재생과 수중 플라즈마를 결합한 화학적 방법으로 폐활성탄 재생특성을 비교하여 다음과 같은 결론을 얻었다.
화학적 방법 단독재생과 수중 플라즈마를 결합한 화학적 방법 모두 화학약품(NaOH, 에탄올)의 함양이 증가할수록, 그리고 재생반응시간이 증가할수록 요오드 흡착력이 증가하였다. 다만, 화학적 재생만으로는 신탄의 요오드 흡착력(954 mg/g) 대비 최대 69%까지 달성할 수 있었다. 화학적 재생에 수중 플라즈마(600 W)를 결합한 경우 화학약품만으로 재생한 경우에 비해 흡착력이 7~24% 높게 나타났다. 재생활성탄 품질기준 2등급 수준(80% 이상)을 달성하기 위해서는 수중 플라즈마(600 W)를 방사하며 NaOH 12%, 에탄올 30%를 주입하고 36시간을 반응해야 한다. 약품주입량 NaOH 20%, 에탄올 50% 조건에서 48시간 반응시킨 경우 요오드 흡착력 회복률 89%를 나타내어 1등급(90% 이상)에 가까운 재생효율을 확인하였다.
흡착이 잘되는 소수성 유기물의 경우 신탄과 폐탄의 제거능에서 큰 차이를 나타내지 않았으나, 소수성이 약한 아미노산과 탄수화물 영역의 유기물은 재생탄의 흡착력이 신탄에 비해 낮게 나타났다.
재생과정을 통해 활성탄의 경도가 어느 정도는 약해지는 것을 발견하였는데, 재생효율이 높을수록 활성탄에 가해지는 손실 정도가 높아져 경도가 최대 7% 가량 낮아졌다. 본 연구에서 평가된 방법을 활용하기 위해서는 재생 후에도 활성탄의 경도를 유지할 수 있는 방안에 대한 추가연구가 필요할 것으로 사료된다.
Acknowledgements
본 연구는 산업통상자원부의 “글로벌전문기술개발사업(섬유생활스트림간협력기술개발사업)”과 환경부의 “차세대 에코이노베이션 기술개발사업(2016002130004)”의 연구비 지원으로 수행되었습니다.